“In the world of industrial manufacturing, the choice of production method can make or break a product’s...
Discover our 100% integrated foundry and our know-how
Located in the heart of maritime Picardie (North of France), Foundry
Davergne designs and manufactures Aluminium-Bronze components
for cutting edge of technology sectors
Industrial
valves
Products for firefighting equipment, water treatment, fluid transport...
Locksmithing,
hardware, building
Access control, armored
door, panic hardware, push
bar, keys, gate accessories...
Railway
Catenary items, wire clamps, current collection arms, parts for TGV, metro, tramway…
Mechanical and engineering industry
Components for industrial equipment, lifting and handling equipment, safety devices…
electricity and energy
Equipment for high-voltage networks, grounding circuit, electrical connection, connecting terminal...
APPEARANCE AND luxury PARTS
Mirror parts, parts decorative items, cookware, buckles for riding, ornament, leather goods...
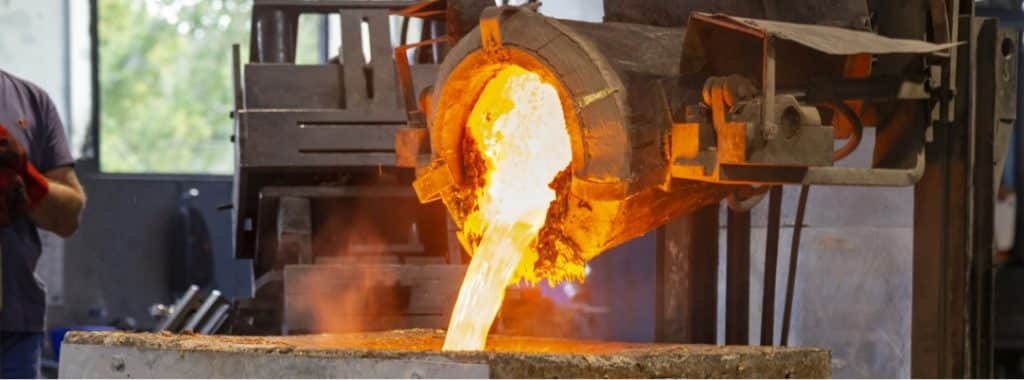
Foundry Davergne, it's
+ 1000 tons of copper alloys produced annually
A team of 125 skilled professionnals
An infinitely recyclable alloy !
No more welded steel or stainless...
The casting process is the most economical alternative process to welding for your series.
Aluminium-Bronze, the corrosion-resistant alternative alloy to medium-hard steel.
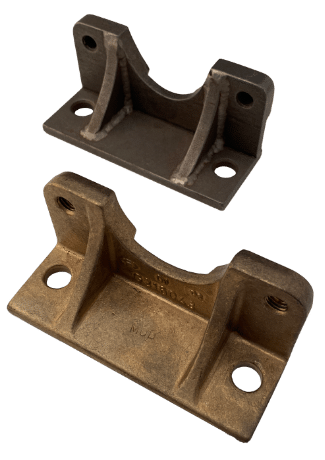
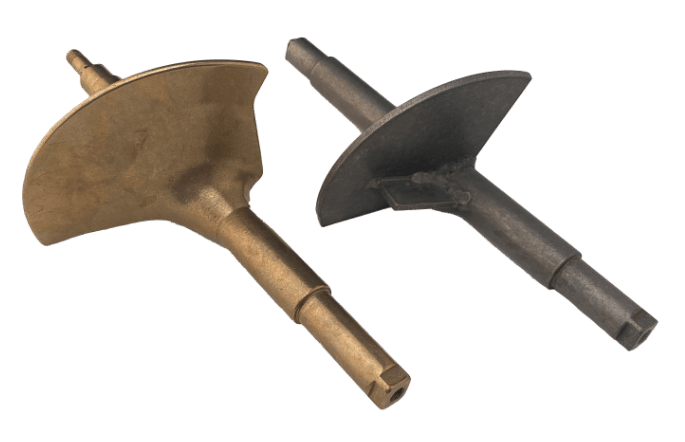
Fully integrated company, from the study and design of your tools to the machining and finishing of your parts
Foundry
Integrated
tooling
Cutting
Machining
Design office
Quality control
Foundry Davergne
High-performance machine park, innovative industrial process…
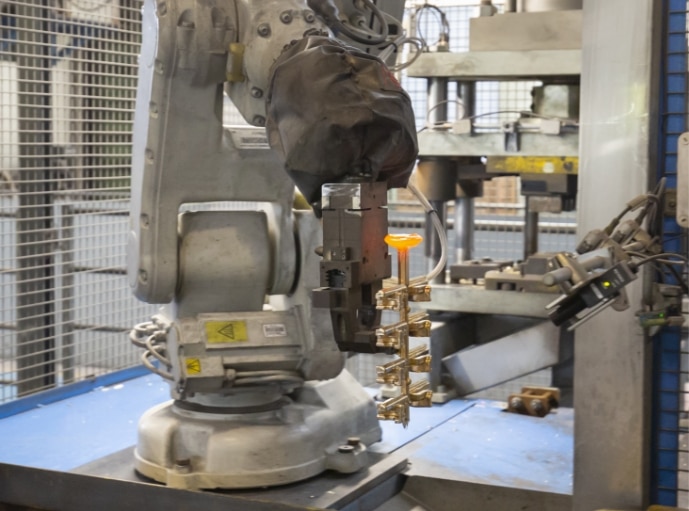
A fully integrated factory from the design of your tools up to the machining of your parts
Since 1947, Fonderie DAVERGNE has continuously evolved in the development of following Aluminium-Bronze alloys: CuAl9, CuAl10Fe2, CuAl10Fe5Ni5. These alloys exhibit excellent mechanical characteristics, equivalent to medium-hard steel. Their exceptional castability allows the creation of complex and precise forms, reducing or eliminating the need for machining operations. It is possible to cast pieces ranging from a few grams to around fifteen kilograms using shell molding.
A high-end Copper alloy for your components
Aluminium-Bronze offers excellent long-term stability and resistance to stress corrosion cracking. It is immune to atmospheric attacks and salt corrosion. Combined with good elastic resistance, this enhances the lifespan of your components.
All our production is carried out in gravity shell casting in metal mold, which improves the mechanical characteristics thanks to rapid cooling due to the good conductivity of the molds. Shell molding is suitable for small repetitive series of a few dozen parts to medium and large-scale production.
The tight and consistent dimensional tolerances associated with shell casting lead in reduced machining operations and a decrease in the weight of the parts.
Our alloys are refined in our melting furnaces using 100 %- recycled copper and aluminium, with or without the addition of iron and nickel.
Metallurgical quality and the internal alloy manufacturing process garantee an optimal material certified by our in-house analysis laboratory.
Continuous search for improvements for even more customer satisfaction
Mold maintenance in our integrated workshop, as well as their cleaning through cryogenics, ensures their longevity.
Our expertise in the production of Aluminium-Bronze components secures your installations across various industries: from railway sectors such as catenary items and components for rolling stock of metros, tramways, and high speed trains, to electrical industry, locksmithing, building, infrastructure, energy, industrial valves, marine industry, water treatment, fluid transport, firefighting equipment, ornamental pieces, and luxury components…
Discover our latest news
The Precision of Lost-Wax Casting Soon Combined with Bronze-Aluminium “Fonderie DAVERGNE is preparing for its future starting...
Fonderie DAVERGNE participation at GLOBAL INDUSTRIE LYON 2025 Fonderie DAVERGNE was delighted to participate in the GLOBAL...
Did you know ?
The Egyptians used the hieroglyph Ânkh to associate it with the terms ‘Life’ and ‘Longevity.’ This Ankh Cross was often crafted in Copper, an alloy already well-known for its exceptional durability
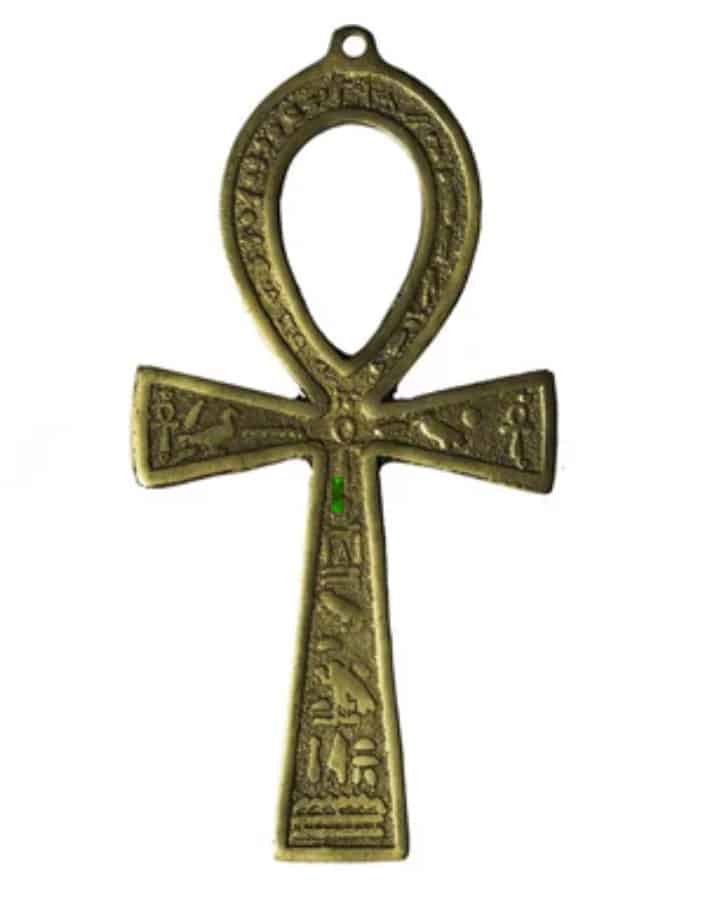
According to archaeologists,
Copper tubes used for water transportation were first employed in ancient Egypt around 2,750 BCE. A specimen from the temple near the Sahure Pyramid in Abusir is on display at the Berlin Museum. Despite the deteriorated state of the structure, the fact that the copper piping is still in good condition serves as evidence of the durability of copper as a piping material..
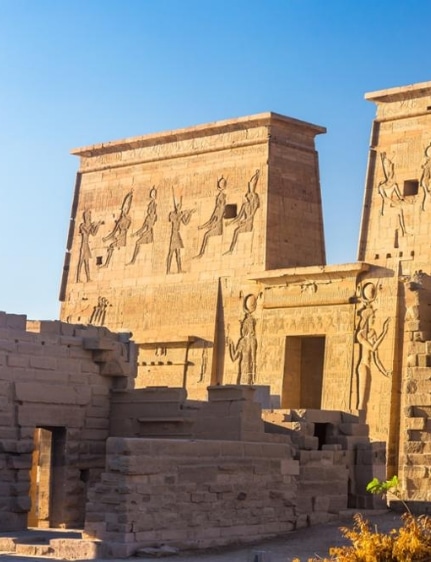