“In the world of industrial manufacturing, the choice of production method can make or break a product’s performance, cost-efficiency, and longevity” confirmed Patrick DAVERGNE, the Technical Director of Etablissements R. DAVERGNE.
When the switch of manufacturing process makes sense…
Welding production method:
One of the first choice of production method at the beginning of an industrial project. Metal plates, tubes, or profiles are assembled through welding & machining.
While this method is favored for its accessibility & flexibility, it faces soon with limitations in terms of complexity, weight, long-term durability & reproductibility.
Die casting method:
Casting involves pouring molten metal into a metallic mold to create a solid part. This process allows for the creation of complex geometries in a single piece, eliminating the need for multiple components and welds.
Key Advantages of Casting
Design flexibility & complexity
- Cast parts can be designed with intricate shapes & internal features that are hardly or costly to achieve with welded assemblies
- Ideal for optimizing mechanical performance & reducing material usage
- Ideal part reproductability from the first casting to the last one as the same casting mould is used
Weight reduction
- By eliminating unnecessary weld reinforcements and overlapping materials, casting allows for lighter components without compromising strength.
- Especially beneficial in sectors like transportation like Railway where every gram counts.
Improved mechanical properties
- Welds are sometimes the weak points in welded assemblies. Casting eliminates these joints, resulting in more uniform strength & fatigue resistance.
- Copper based alloys like CuAl10Fe2, offered by Fonderie Davergne, offer excellent resistance to corrosion and wear.
Cost efficiency
- Fewer parts, fewer welds, and less machining mean lower labor and production costs.
- Reduced need for quality control on welds and assemblies.
Enhanced Aesthetics & Integration
- Cast parts have smoother surfaces & can integrate branding or functional features directly into the mold.
- No visible welds or seams—ideal for consumer-facing products.
Sustainability
- Less material waste and energy consumption compared to cutting and welding
- Recyclable alloys & optimized production processes reduce environmental impact
- Copper based alloys like CuAl10Fe2 are lead free & zinc free -> good for our environment
A concrete example of what has been already done?
At Fonderie Davergne, the transition to casting is a reality since 1947. More than a technical upgrade—it’s a commitment to excellence. Thanks its fully integrated foundry (Casting shop & machining shop at the same place), Fonderie DAVERGNE could recently produce & deliver a high-performance component tailored to a demanding actor of the Railway Industry.
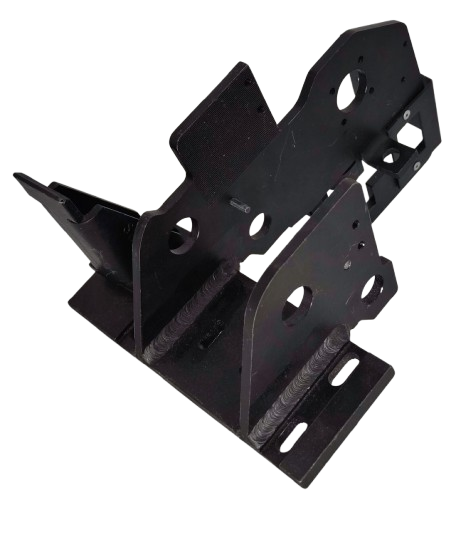
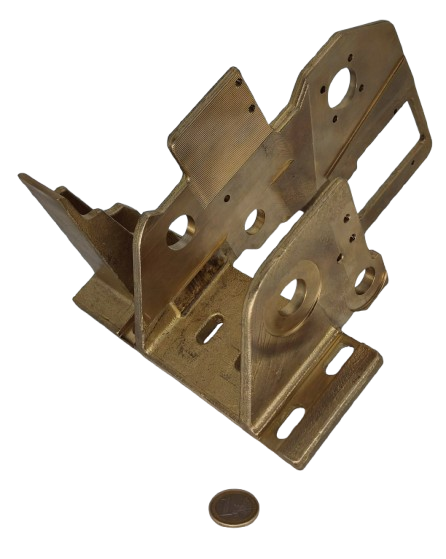
And now? Are you ready for the switch?
Switching from Welded assemblies to casting isn’t just a change in process—it’s a leap toward smarter, leaner, and more resilient manufacturing.
Whether you’re in rail, energy, defense, or heavy industry, casting offers a future-proof solution that aligns with modern engineering demands.
If you’re considering this transition, now is the time to explore how casting can elevate your production strategy.

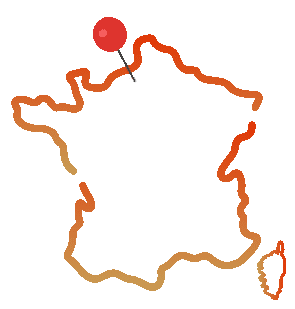